Regenerative Thermal Combustors
Volatile Organic Substances (VOCs) generated in production activities contain organic substances, including toxic substances.
To contain and control atmospheric emissions, filtration treatment is needed to ensure that the air stream is free of these elements.
Regenerative thermal purification is the answer to this problem both in terms of quality of result and operating cost, allowing such a high thermal recovery of flue gasthat this solution is extremely competitive.
Theoxidation of VOCs (Volatile Organic Substances) is carried out in the thermally insulated combustion chamber at a temperature of 750 -850° C; it is possible to reduce the concentration of COT at the outlet to values of 5 -20 mg/Nm3. The heat required to heat the combustion chamber (during start-up) and to maintain the combustion temperature is provided by a supply fuel, usually natural gas or LPG.
The oxidizers are referred to by the term "regenerative" in that the heat from the flue gas exiting the combustion chamber is used to preheat the ceramic masses contained in a first heat exchange tower; the incoming flue gas, passing over a second exchange tower that is already at temperature, in turn exchanges the accumulated heat provided by the hot flue gas that has already been purified. The third stand-by chamber ensures that there are no peaks of COT concentration in the atmosphere during the inversion phase of the chambers.
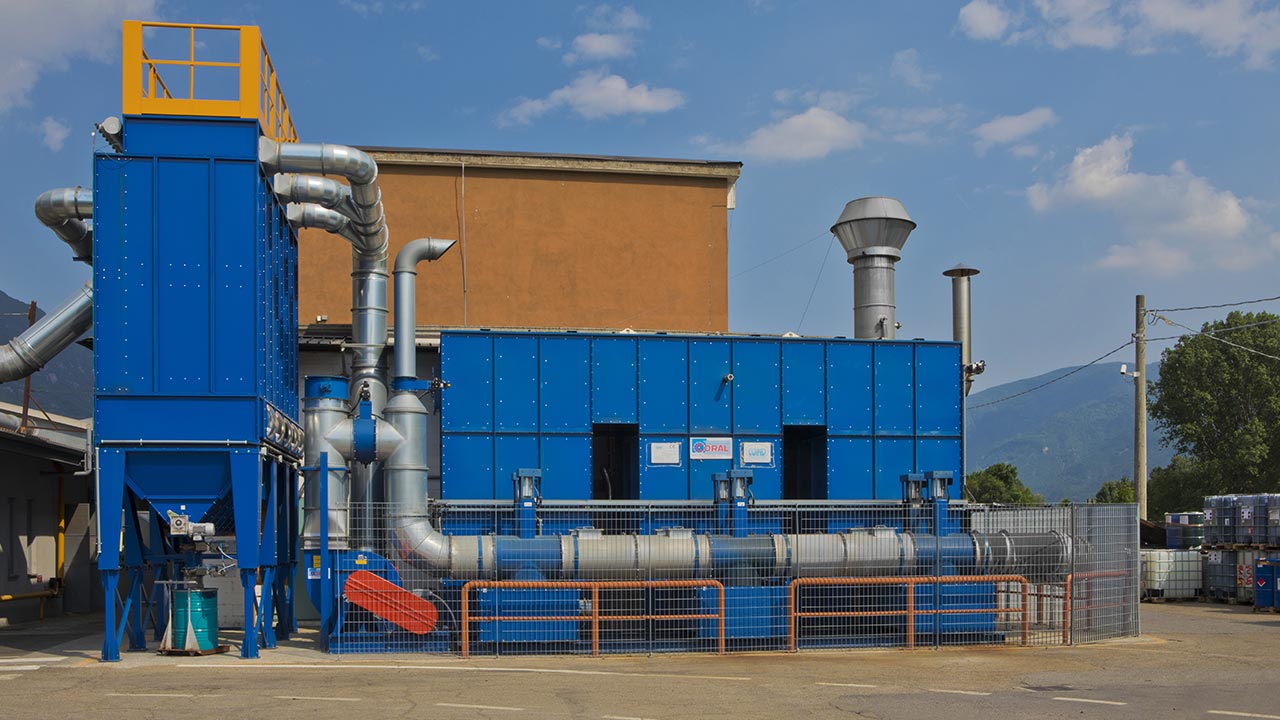
The dimensional criteria are given in Table 1 "Minimum requirements for thermal and catalytic combustion systems" of UNI 11304-2:2008, transposed in sheet PC.T:02 of BAT Lombardy (D.g.r. May 30, 2012 - no. 3552), in particular:
Dwell time
Calculated residence time in the burner zone between the masses of the two towers:
- In the absence of chlorinated VOCs: time > 0.6 s
- con Cloro < 0,5 %: tempo > 1 s
- With chlorine between 0.5 % and 2 %: time > 2 s
Minimum operating temperature:
- in the absence of chlorinated VOCs: 750° C
- con Cloro < 0,5 %: 850° C
- With chlorine between 0.5 % and 2 %: 950° C
Number of rooms
The number of chambers can vary depending on the type of pollutant and flue gas flow rate. The most common configurations are:
- Bi-chambers: consist of two heat exchange towers, during the inversion of the IN/OUT cycle there are a few seconds during which the flue gases do not pass into the combustion chamber so, since they are not oxidized, they generate a peak emission at the stack. This drawback can be remedied by adopting a compensation chamber into which to send the flue gases at the time of chamber inversion.
- Tri-chamber: consist of three heat recovery towers, two sections are always in service and the third is on stand-by. This configuration allows flue gases that have undergone the complete oxidation process to be sent to the stack.
Terms of use
Continuousprocessing (and emission) cycle on 24h, and on at least 5 days/week.
Concentration of pollutants (SOVs) is high (even on the order of 1-2 g/Nm3) combined with low flue gas flow rates.
Dust flow of less than 5 mg/m3 and a flammable VOC content of less than 25 percent at the L.E.L. Any organic substances in vapor form must be condensed before being sent to the CTR through appropriate inertial filters and/or cyclones.
It is possible/necessary to pretreat the emission to reduce the dust content: coalescing or scrubber systems can be used. Protection of the suction and combustor lines with suitable ATEX systems may be required.
Operating parameters
Flue gas temperature IN: depends on the type of dedusting system, if any.
Fuel consumption: on existing 10,000 Nm3/h plants, 18 to 22 Nm3/h of methane is consumed at steady state, in the absence of pollutant.
Combustion temperature 750 -800°C
Flue gas temperature OUT: ≈ 80 to 100°C higher than the inlet temperature.